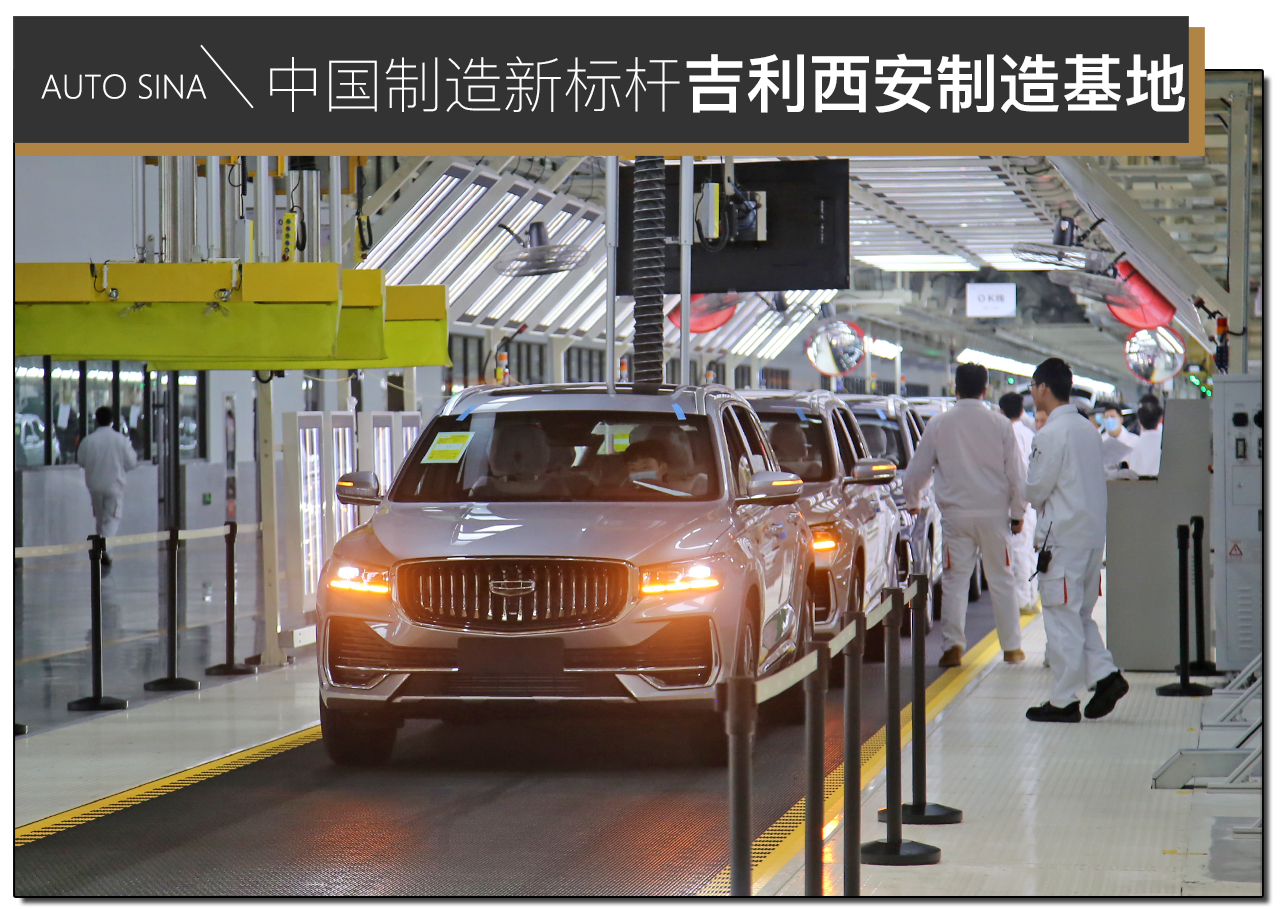
As a benchmark model in the era of 4.0 car-building, it has been recognized by the market in terms of product strength. It has sold 26,263 vehicles in more than two months, and the current order exceeds 60,000 vehicles. The R&D and manufacturing strength behind it must have been completely changed. The answer is Geely Super Intelligent Black Lamp Factory in Xi ‘an.
Brief introduction of Xi’ an manufacturing base
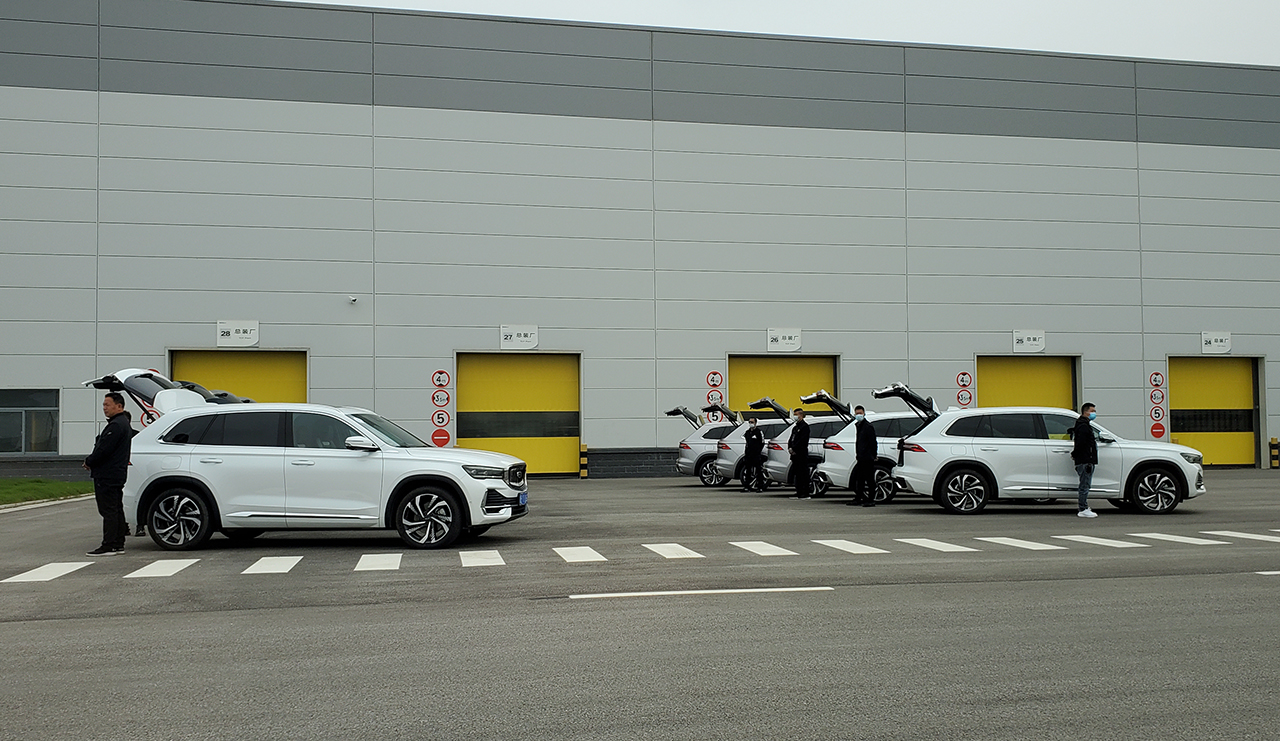
Xi’ an manufacturing base is Geely Automobile’s vehicle production base with the largest area, the largest investment, the highest products, the most advanced technology and the highest degree of intelligence. It covers an area of 2,260 mu, with a total investment of over 10 billion. It has four workshops: stamping, welding, painting and final assembly, with a maximum annual production capacity of 360,000 units, integrating digitalization, automation, intelligence and flexibility.
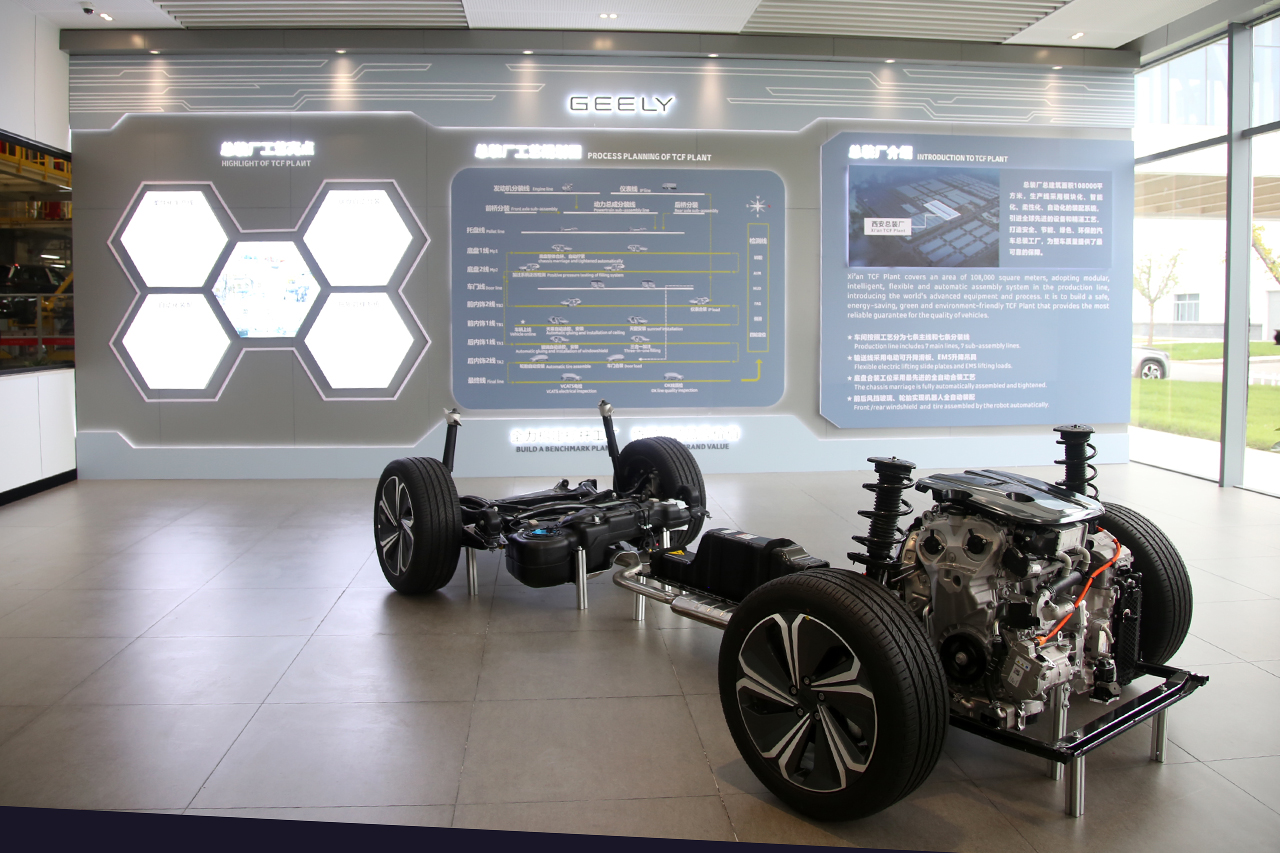
At present, only "China Star" series flagship model Xingyue L is produced. The factory planning supports the production and manufacture of CMA and SEA models with vast architecture, and meets the flexible, automatic and intelligent collinear production of 6 models on 3 platforms. The automatic turntable and switching library are used to switch models, which can be completed within 1 minute. It covers electric vehicles, hybrid vehicles and fuel vehicles.
Xingyue L ushered in the 30,000 th off-line ceremony.
On October 13th, Xingyue L ushered in the 30,000th off-line ceremony at the manufacturing base in Xi ‘an, Jili. In the past September, the sales volume of Xingyue L reached a new high, reaching 10,168 vehicles. After more than two months of listing, the cumulative sales volume was 26,263 vehicles, and the current orders exceeded 60,000 vehicles. In order to meet the needs of consumers, a new two-wheel drive intelligent model was added, with a guiding price of 163,200 yuan, shortening the delivery cycle from 90 days to 45 days.
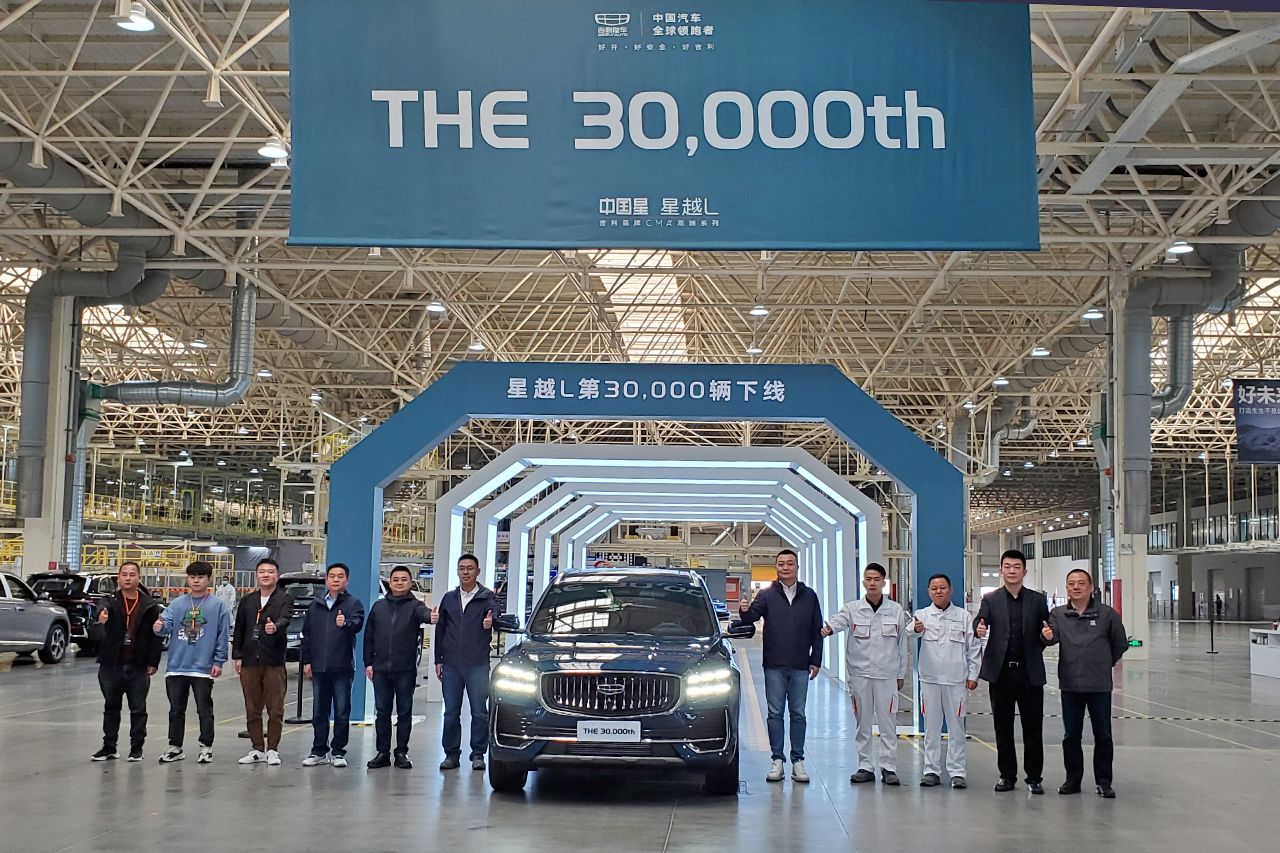
As the flagship series of Geely brand, "China Star" achieved a sales volume of 21,520 vehicles in September, accounting for 25% of the sales volume in the product matrix of Geely brand. Among them, "China Star Flagship Family Car" Xingrui sold a total of 10,173 cars in September, and 95,726 cars in the first nine months of this year. The total sales volume has exceeded 110,000 cars in the 11 months since its listing.
What is a black light factory?
Xi ‘an manufacturing base has a full-process manufacturing plant, including stamping, welding, painting and final assembly. At present, there are less than 2,000 employees in Xi ‘an manufacturing base, which is about half of the average factory. High intelligence and automation are the basis for the realization of the black lamp factory.
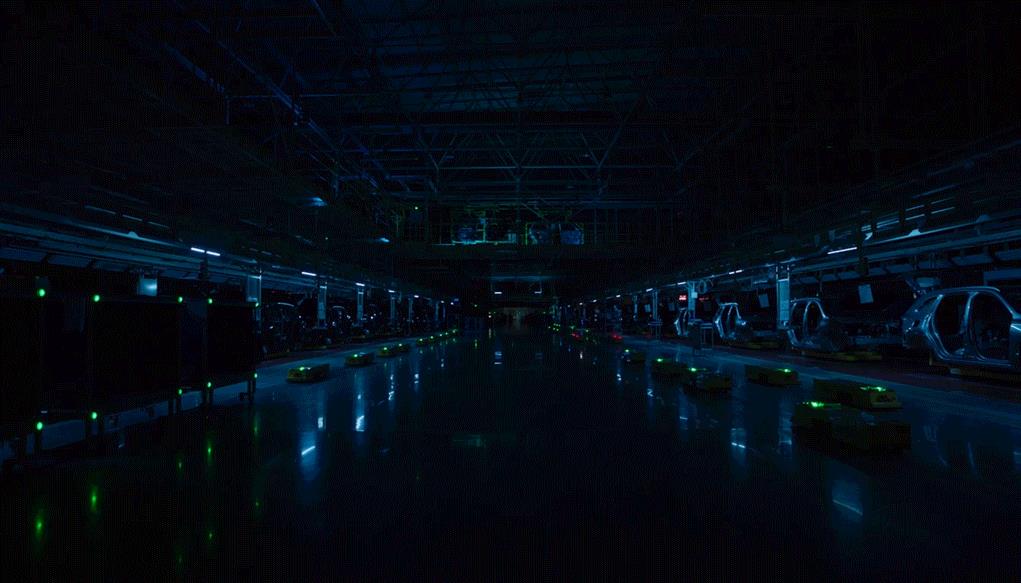
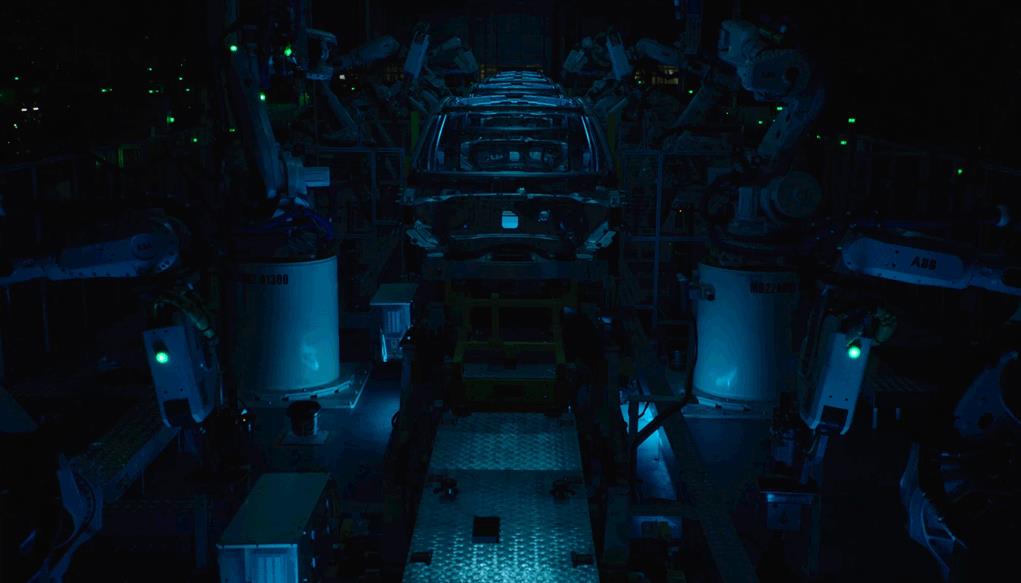
Among them, stamping: materials from unstacking, feeding, cleaning, two-piece separation, compressor transmission, until the stamping parts are off-line, are all realized by automation: welding: the automation rate is 100%, and the "Apras welding process" unique to luxury cars and the industry-leading laser fusion welding process are also applied.
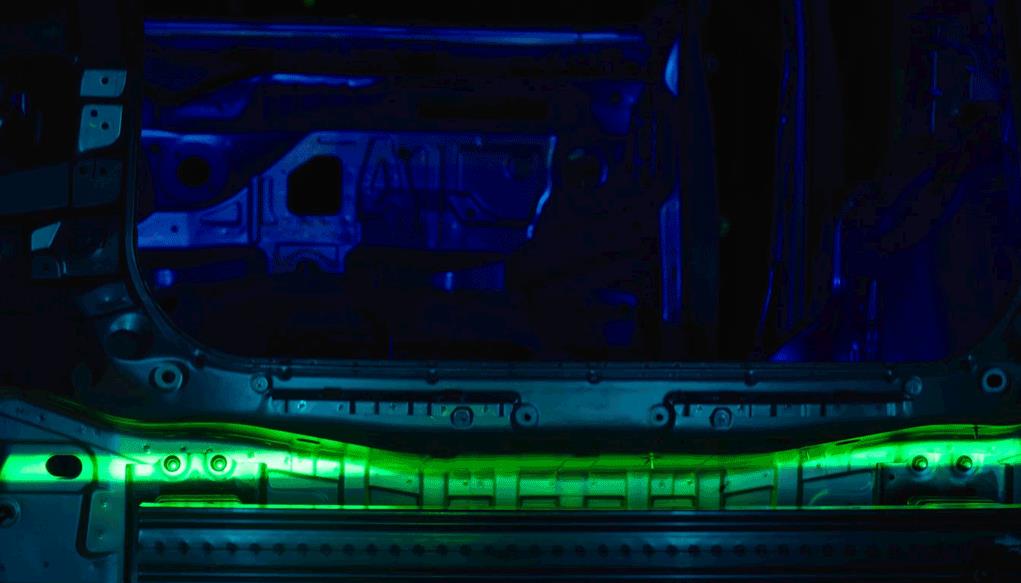
Painting: pretreatment electrophoresis, sealing and topcoat are three stages, and 120 sets of robot systems are connected in series to realize full-automatic production, adopting the world’s most advanced and environmentally-friendly B1B2 water-based intermediate coating-free process; Final assembly: the chassis is assembled automatically to realize the automatic assembly of the car body and chassis at one time, and the front and rear windshield and tires are assembled automatically without people.
The stamping workshop is fully automatic, and the die can be changed automatically in 3 minutes.
The stamping workshop has a total construction area of about 27,000 square meters. The production line adopts the products of international first-class enterprises, uses advanced technologies such as dust prevention and noise reduction, automatic handling, one-button die change and so on, and adopts AGV transportation system for finished product transportation. It is a leading stamping production line in China.
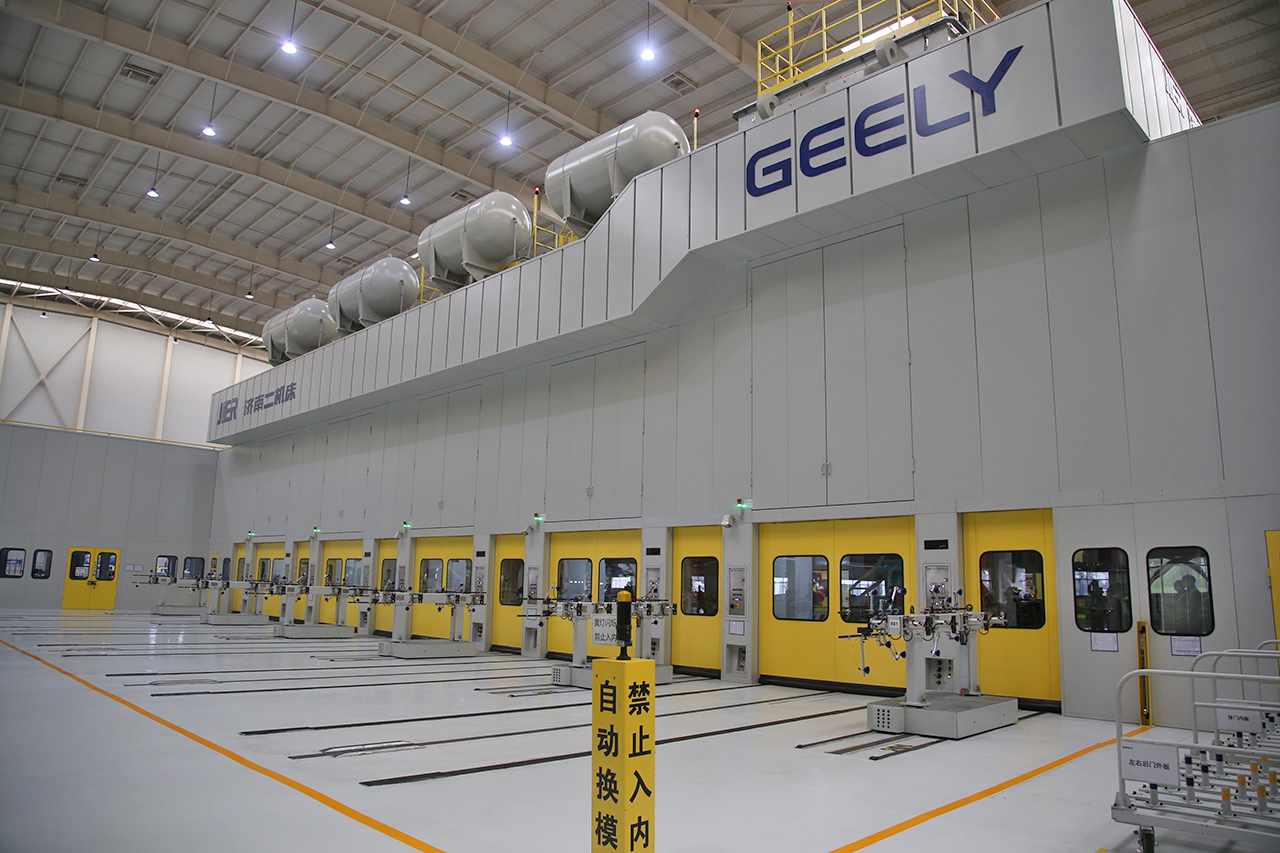
The stamping workshop is equipped with 12 presses, and it is planned to have three high-speed stamping lines: Line A and Line B are put into production, and Line C is a reserved production line. The stamping process is fully automatic, and the whole line is closed to prevent dust and reduce noise, and the noise is less than 85dB. Production of steel-aluminum mixed line: the first line is equipped with German SMT wet cleaning machine and Wandres dry cleaning machine, and the stacking is also equipped with air knife, and the waste line is reserved for aluminum plate transmission. The production of aluminum plates can be switched at any time to meet the production requirements of lightweight car bodies. The whole line can realize automatic die changing in three minutes.
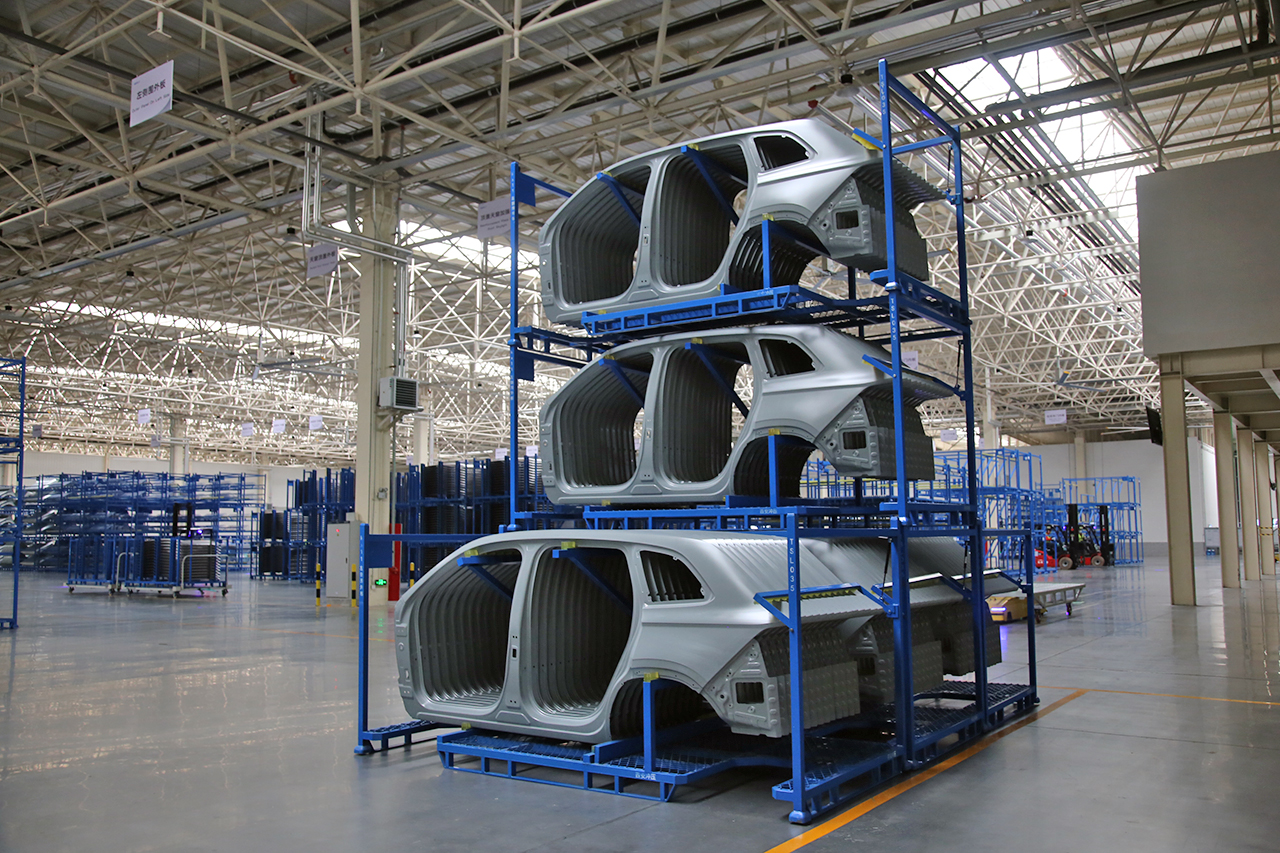
Intelligent unmanned transportation system: AGV is equipped at the end of the line, which can be put into storage with one button. Through the dispatching management system, the stamping parts can be transferred automatically by cruising, and it has the functions of automatic charging, dormancy and awakening. Three-dimensional warehouse: the workshop is equipped with intelligent three-dimensional warehouse, and WMS storage system is adopted. One-click operation can complete the loading and unloading of end pickers, and the three-dimensional storage space can improve the storage utilization rate by 400%.
Welding workshop introduces high-end car welding technology.
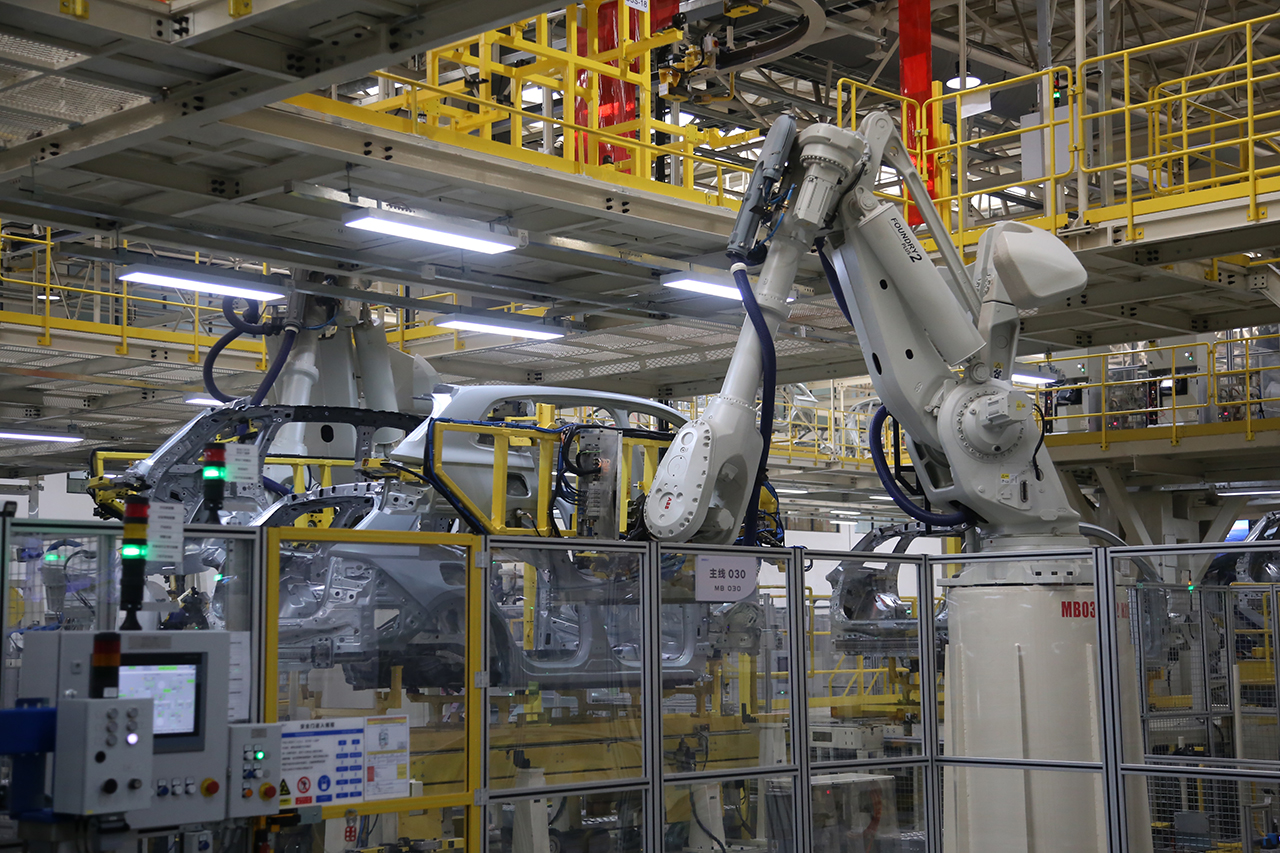
The welding workshop covers an area of 91,000 square meters. There are 585 robots in the whole workshop, and the welding automation rate can reach 100%, including 11 advanced manufacturing processes, such as spot welding, projection welding, stud welding, Arplas welding, laser welding, laser cutting, MAG/MIG welding, riveting, online punching, edge rolling and press edging. It has the flexible collinear production capacity of 5+1 vehicles and the production cycle can reach 60JPH.
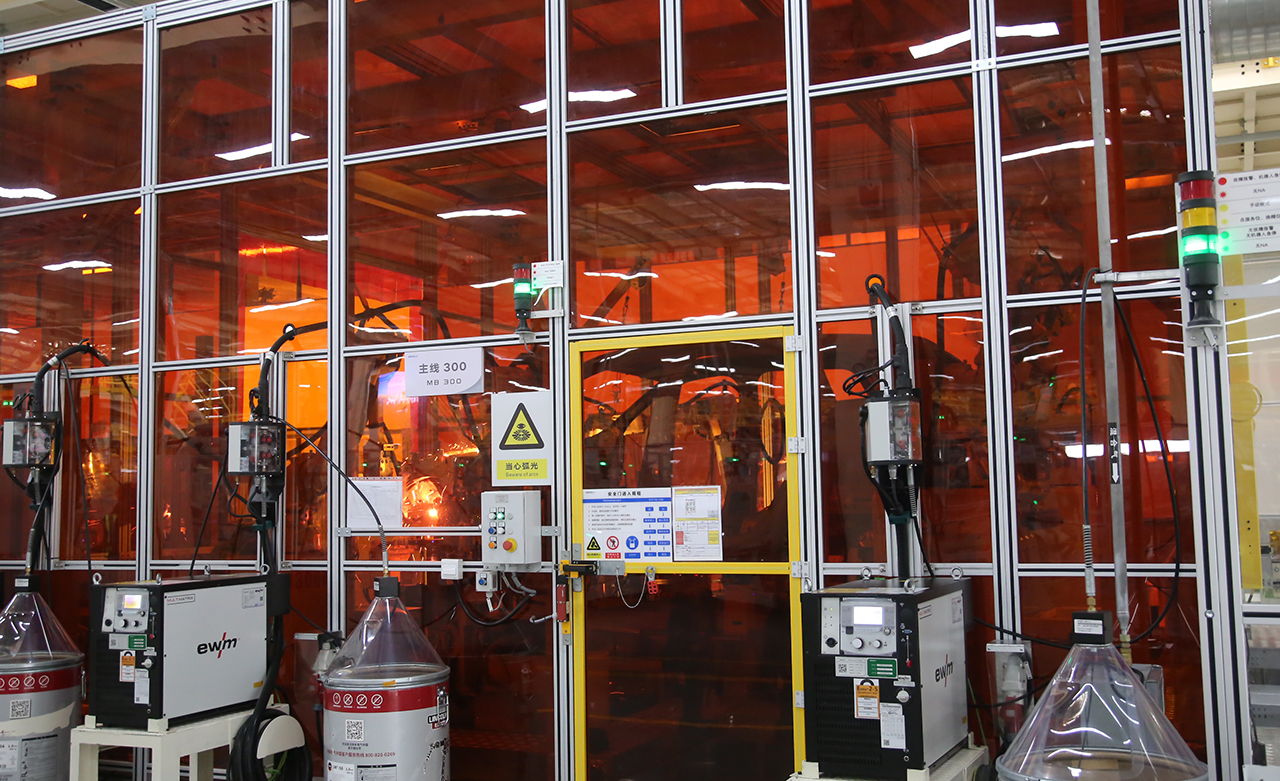
ISV cluster flexible vehicle line measuring system: The main line measuring station adopts ISV cluster flexible vehicle line measuring system, which can complete 100% measurement of 235 key measuring points of the vehicle body and store data for accurate monitoring of the dimensional stability of the vehicle body.
The painting workshop adopts B1B2 water-based intermediate coating-free process for waste gas recovery and treatment.
Covering a total area of 33,000 square meters, it mainly undertakes tasks such as body anticorrosion/sealing, NVH (sound insulation and noise reduction) and spray decoration. More than 2,000 process parameters, more than 150 energy consumption parameters and more than 1,000 equipment parameters in the whole workshop can be monitored automatically and in real time. Fully enclosed operation can effectively reduce employees’ occupational injuries and environmental pollution.
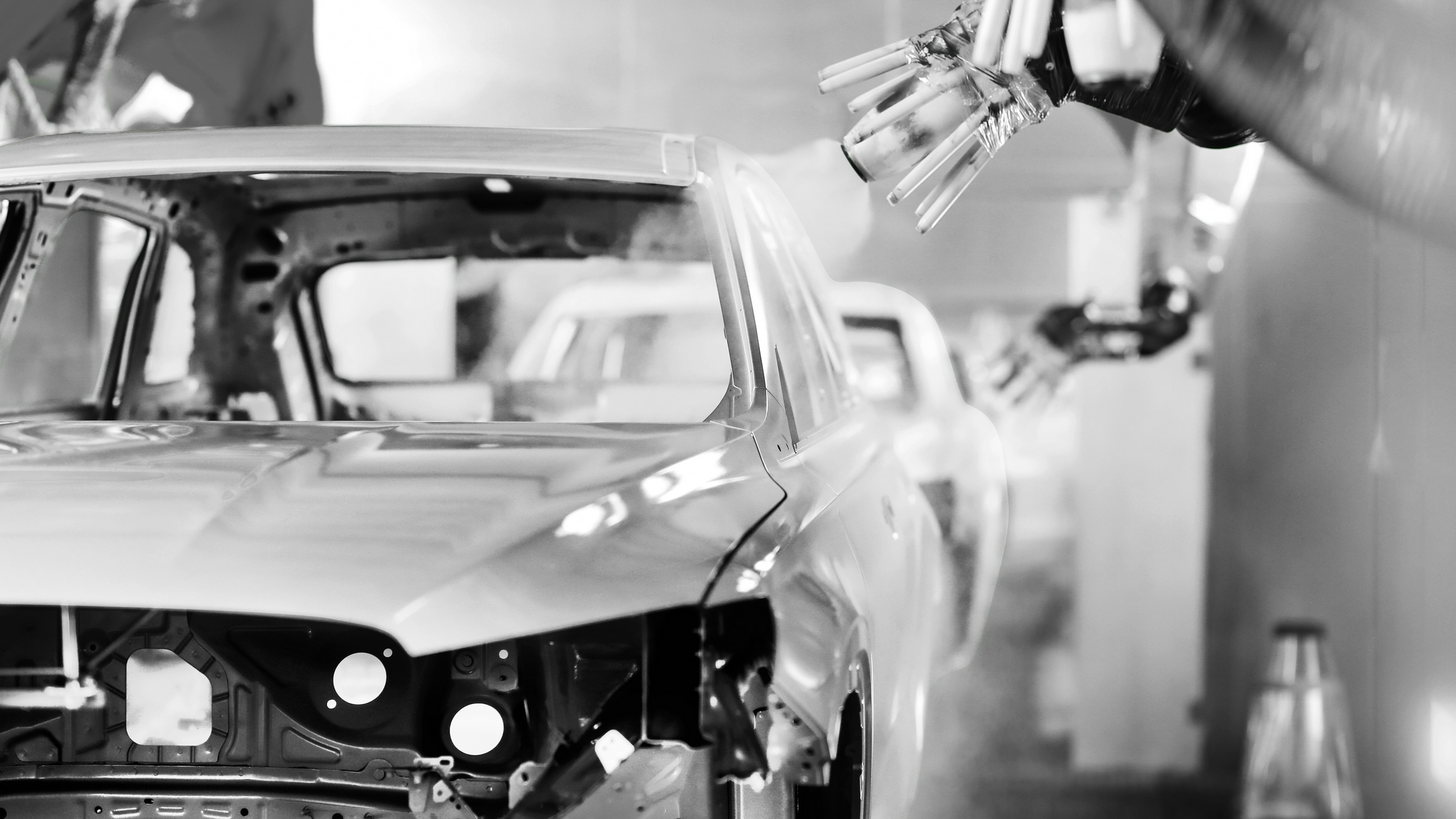
Body topcoat adopts the world’s most advanced B1B2 water-based intermediate coating-free process, and compared with the traditional process, the emission of VOCs (volatile organic compounds) is reduced by 30%. 36 robots realize automatic gluing; Waste gas treatment device: the coating waste gas is incinerated by concentrating wheel+RTO incineration system and TNV incineration system, so as to ensure that the VOCs emission is less than 30 mg/m and the heat energy recovery rate is over 95%.
Real-time monitoring data record of chassis automatic assembly in assembly workshop
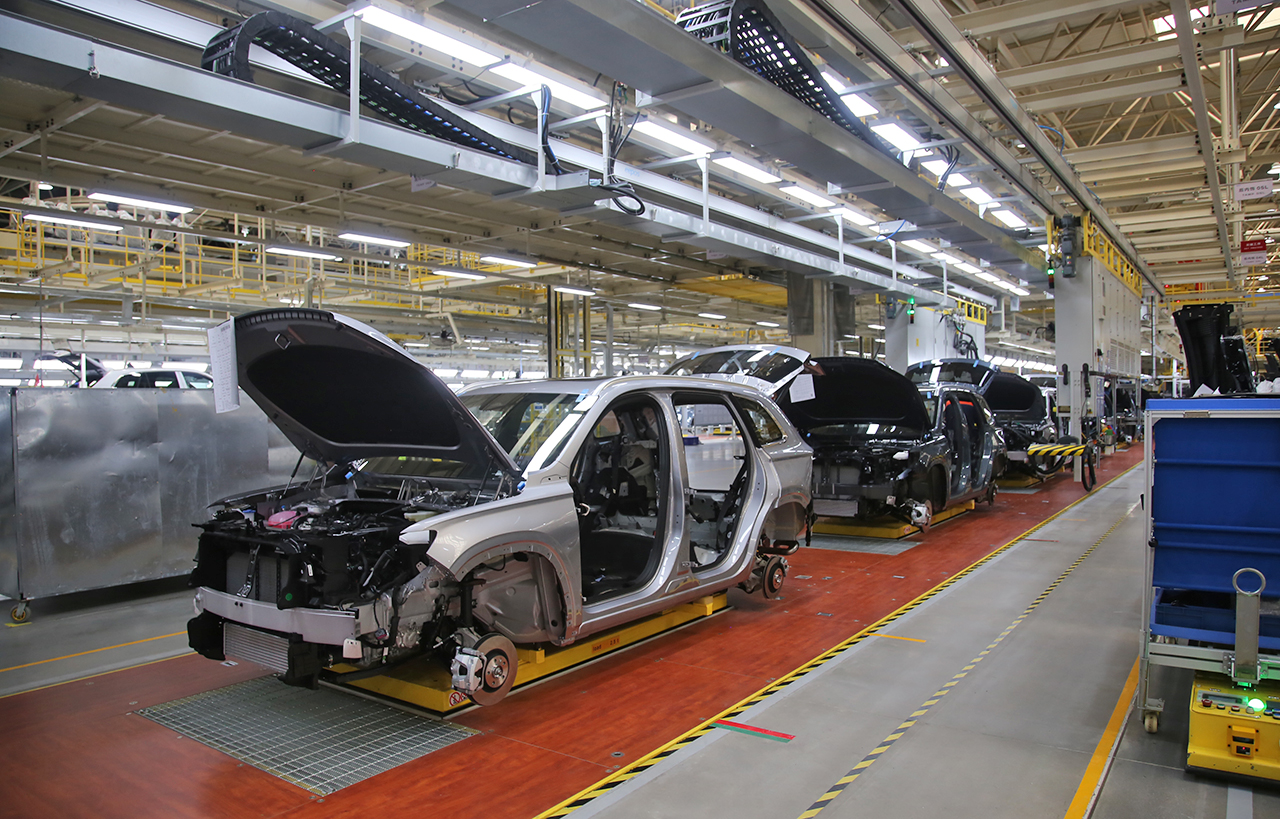
The general assembly plant has a total construction area of 108,000 square meters, and the production line adopts a modular, intelligent, flexible and automatic assembly system, which improves automation, and at the same time, it also has humanized equipment for employees to operate, reducing production intensity and improving safety.
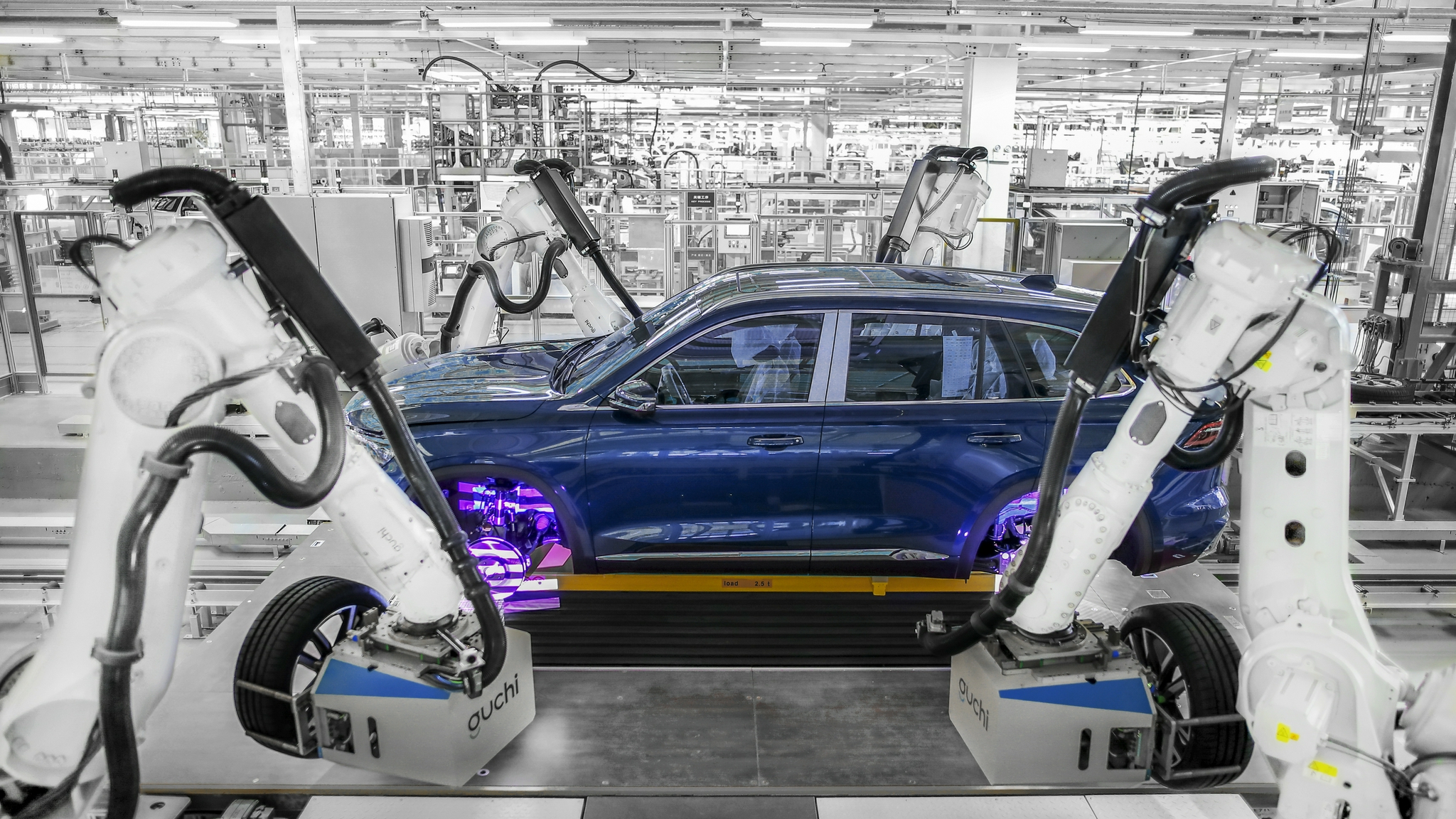
The whole chassis is automatically assembled to realize the full-automatic one-time assembly of the vehicle body and chassis, and the high-precision servo tightening shaft realizes the synchronous tightening of chassis mounting points, which can meet the requirement that 30 bolts can be tightened synchronously within 16s, and the tightening positioning accuracy is ±0.25mm;; The windshield gluing installation and tire installation all adopt unmanned automatic installation.
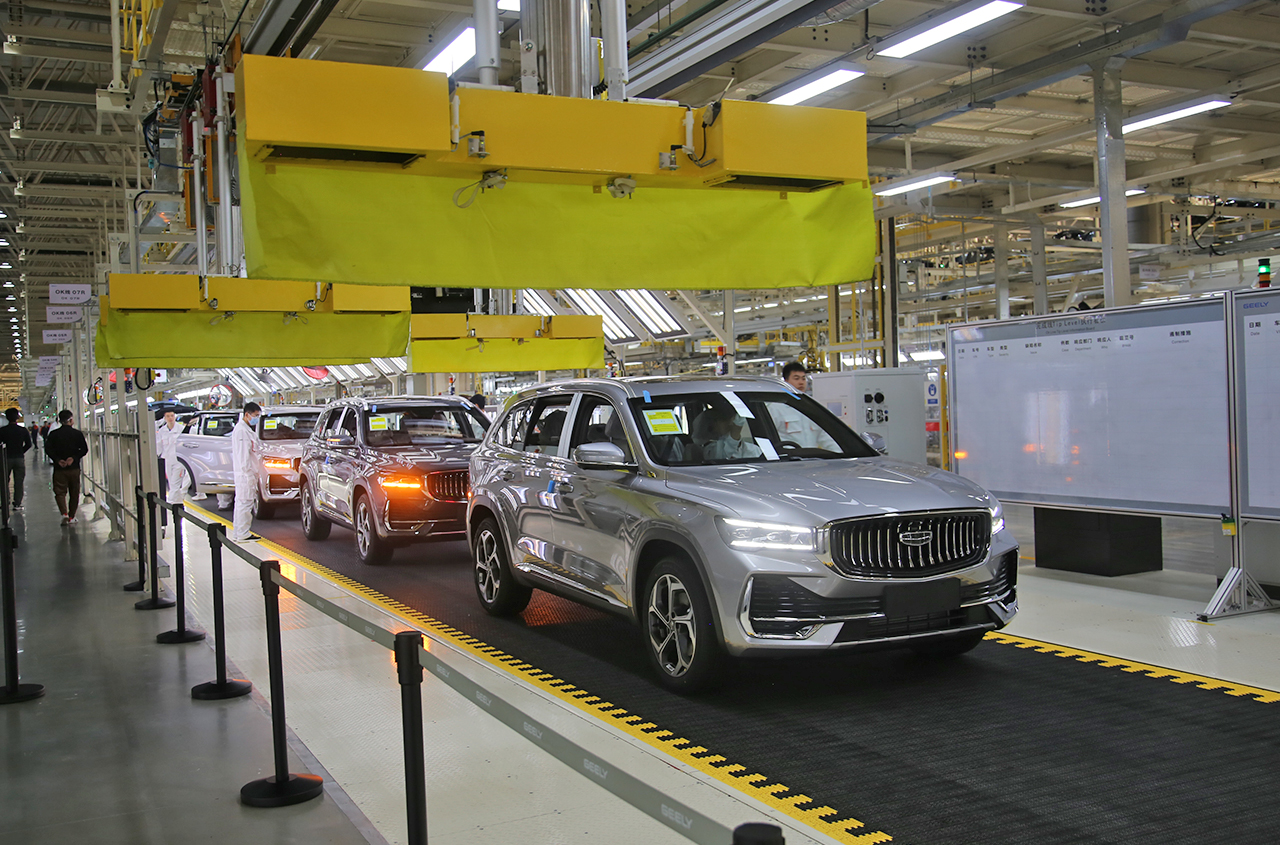
Intelligent, interconnected and efficient torque management system is introduced. All assembly torques have closed-loop control, realizing the functions of real-time control and data recording in the assembly process. EPS tightening error prevention system provides complete process error prevention.
Self-sufficient ecological factory
Whether it is carbon neutrality and peak carbon dioxide emissions’s long-term goal or energy and environmental protection indicators, Xi ‘an factory is a green ecological factory with zero pollution in its life cycle.
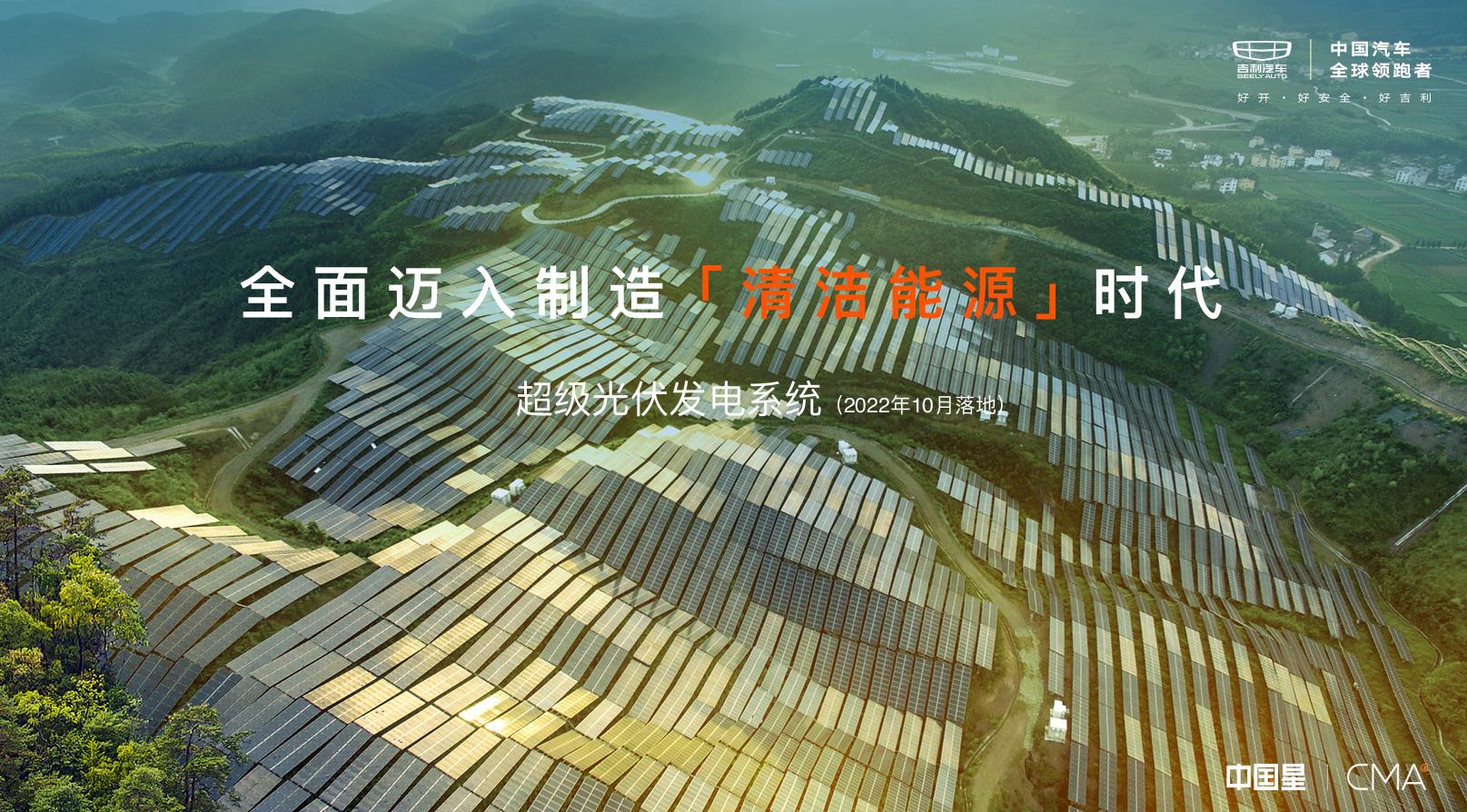
It realizes the "three zero" green circulation system in the manufacturing cycle: 0 waste water discharge, 0 waste landfill and 0 harmful substance discharge; It will have a 400,000 ㎡ super photovoltaic power generation system with a total investment of 264 million yuan, which will be completed in 2022. The annual power generation is 66 million kwh, saving 25,072 tons of standard coal and reducing 62,482 tons of carbon dioxide. The energy emission reduction effect is equivalent to planting 3,726 hectares of forest.
Comments:The high-standard R&D and manufacturing system brings high-standard car products. Xingyue L is one of the high-end models of Geely brand built under this background. Geely Xi’ an manufacturing base has realized the whole process automation of stamping, welding, painting and final assembly. Digitalization and intelligence have greatly improved the manufacturing standards, and ensured the standardization of each car manufacturing, the traceability of manufacturing processes, etc., reducing the quality defects caused by human intervention. This is what factory manufacturing should look like in the industrial 4.0 era, and it also adds a quality guarantee to Xingyue L.